The Ultimate Overview to Packaging Machine Repair Work: Keep Your Workflow Running Efficiently
Understanding the intricacies of product packaging maker repair work is crucial for keeping ideal performance and minimizing disturbances. Routine upkeep not just extends the life of these equipments however also addresses usual problems that can impede performance.
Significance of Regular Upkeep
Regular upkeep of packaging equipments is vital for making certain optimum performance and long life. By executing a structured maintenance timetable, operators can recognize possible issues prior to they intensify right into significant troubles. This proactive approach not only decreases downtime however additionally prolongs the life-span of the equipment, eventually leading to minimized functional prices.
Routine examinations enable for the analysis of crucial parts such as seals, belts, and sensors. Addressing deterioration without delay avoids unforeseen failings that can disrupt production and cause pricey repairs. Furthermore, regular upkeep aids ensure compliance with market requirements and laws, cultivating a secure working environment.
Furthermore, upkeep tasks such as lubrication, cleansing, and calibration substantially enhance equipment efficiency. Improved performance translates to consistent product quality, which is vital for maintaining customer fulfillment and brand name track record. A properly maintained product packaging maker runs at ideal speeds and decreases material waste, adding to total performance.
Usual Product Packaging Maker Problems
Packaging machines, like any intricate equipment, can come across a range of typical issues that might prevent their efficiency and effectiveness - packaging machine repair. One prevalent trouble is irregular sealing, which can lead to item wasting and waste if packages are not effectively secured. This typically results from misaligned parts or used sealing components
One more frequent concern is mechanical jams, which can happen due to international items, worn components, or incorrect placement. Jams can cause delays in manufacturing and increase downtime, inevitably impacting overall performance. Furthermore, digital malfunctions, such as failing in sensors or control systems, can lead and interfere with procedures to imprecise measurements or unpredictable equipment habits.
Moreover, problems with product feed can also develop, where items might not be delivered to the product packaging location regularly, creating disturbances. Wear and tear on rollers and belts can lead to suboptimal performance, needing prompt attention to prevent more damage.
Comprehending these usual issues is essential for keeping the integrity of packaging operations, making certain that machinery runs smoothly and effectively, which subsequently helps in meeting production targets and keeping product high quality.

Repairing Methods
Effective repairing methods are vital for quickly dealing with concerns that develop with packaging equipments. A methodical approach is crucial for identifying the origin of breakdowns and reducing downtime. Begin by collecting info concerning the signs observed; this may include uncommon noises, functional delays, or mistake codes displayed on the maker's interface.
Following, refer to the equipment's manual for repairing guidelines certain to the model concerned. This source can offer beneficial insights into usual issues and suggested analysis steps. Use aesthetic evaluations to look for loose connections, used belts, or misaligned parts, as these physical factors commonly add to operational failings.
Apply a process of elimination by screening read this post here specific machine functions. If a seal is not forming correctly, evaluate the securing mechanism and temperature settings to figure out if they fulfill functional requirements. Document each step taken and the results observed, as this can help in future fixing efforts.
Repair service vs. Substitute Decisions
When encountered with devices breakdowns, making a decision whether to repair or replace a article packaging machine can be a complex and crucial choice. This decision depends upon numerous crucial elements, including the age of the machine, the level of the damages, and the forecasted effect on functional performance.
To start with, consider the machine's age. Older machines may require even more regular repair work, resulting in higher cumulative costs that can go beyond the investment in a new device. Furthermore, evaluate the extent of the breakdown. Minor concerns can typically be dealt with quickly and affordably, whereas substantial damage could require a significant economic commitment for fixings.
Operational downtime is an additional important factor to consider. If repairing the maker will create prolonged hold-ups, purchasing a new equipment that offers improved efficiency and dependability could be more prudent. Furthermore, take into consideration the availability of components; if substitute elements are difficult ahead by, it might be more tactical to change the equipment entirely.
Eventually, executing a cost-benefit evaluation that consists of both prompt and lasting implications will aid in making an informed decision that aligns with your operational objectives and budgetary constraints. (packaging machine repair)
Safety Nets for Long Life
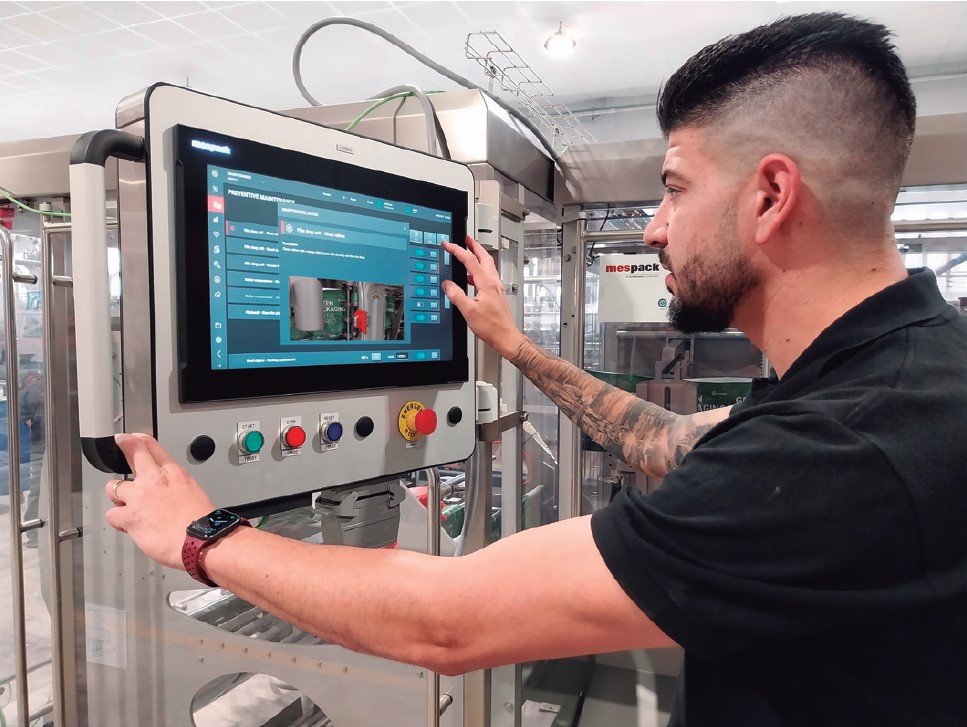
Secret safety nets include routine lubrication of moving parts, positioning checks, and calibration of sensing units and controls. Developing a cleaning schedule to remove particles and impurities from equipment can considerably minimize deterioration (packaging machine repair). In addition, monitoring operational parameters such as temperature and vibration can help spot irregularities early
Educating personnel to identify indicators of wear or breakdown is an additional critical part of preventative upkeep. Equipping drivers with the understanding to carry out basic troubleshooting can result in quicker resolutions and minimize operational disturbances.
Documents of maintenance activities, including service documents and examination searchings for, promotes responsibility and helps with informed decision-making regarding fixings and substitutes. By focusing on safety nets, companies can ensure their product packaging makers operate at peak efficiency, inevitably resulting in increased performance and minimized operational prices.
Final Thought
In conclusion, the reliable upkeep and repair work of product packaging equipments are critical for maintaining functional performance. By executing precautionary actions, businesses can enhance device durability and make certain uninterrupted efficiency in product packaging procedures.
Recognizing the intricacies of packaging device repair work is vital for keeping optimum efficiency and minimizing disruptions.Regular maintenance of packaging machines is essential for you can try these out guaranteeing ideal performance and durability.Packaging devices, like any type of complex machinery, can encounter a variety of common concerns that might prevent their efficiency and effectiveness. If repairing the device will trigger prolonged delays, spending in a brand-new maker that uses improved efficiency and reliability could be extra sensible.In final thought, the effective upkeep and fixing of packaging devices are paramount for maintaining functional effectiveness.
Comments on “Top Packaging Machine Repair Solutions for Enhanced Operational Performance”